Stochastic Modeling of the Interaction of Tool Wear and the Machining Affected Zone in Nickel-Based Superalloys, and Application in Dynamic Stability
An important factor for the aerospace industry is the application of sophisticated materials meeting the high standards with regard to high temperatures and the pressure requirements. With its high level of strength and corrosion resistance, Inconel 718 is such a material. Machining these materials is a special challenge due to its high tool wear and occurring process forces. One possibility to minimize the tool wear and the process forces during machining is the usage of so-called trochoidal milling.
Simulation systems can be used to predict the process as accurately as possible. In addition, the simulation system can be used for the analysis and the process design. Therefore, appropriate models have to be developed, with which, for example, a description of the tool wear evolution is possible. The aim of this project is to analyze the interrelationships between the machining parameters and the tool wear evolution and to investigate their influence on the output machining affected zone (MAZ) depth. Through these fundamental investigations, models will be developed, with which a prediction of the process forces, the stabilities, and the resulting workpiece topographies are possible.
This research project is in cooperation with the Clemson University in South Carolina (USA) and is funded by the German Research Foundation (DFG) on the German side and on the American side by the National Science Foundation (NSF).
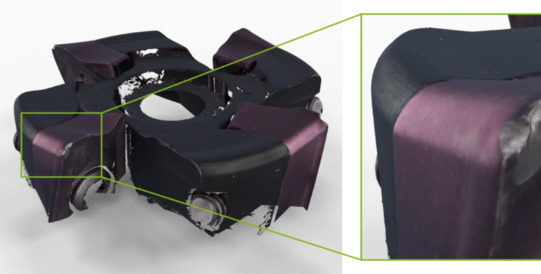
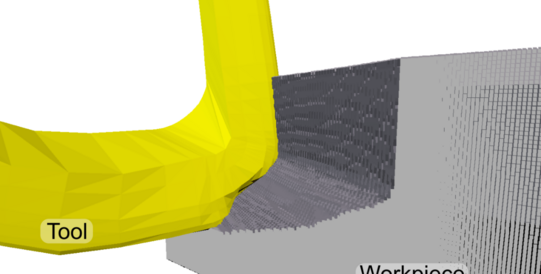